Reis de la innovació
La planta de Hartmann a Montornès del Vallès fa servir la fabricació additiva en 3D per als seus recanvis
La mesura, proposada per un dels treballadors, suposa un estalvi del 80% en el cost de fabricació
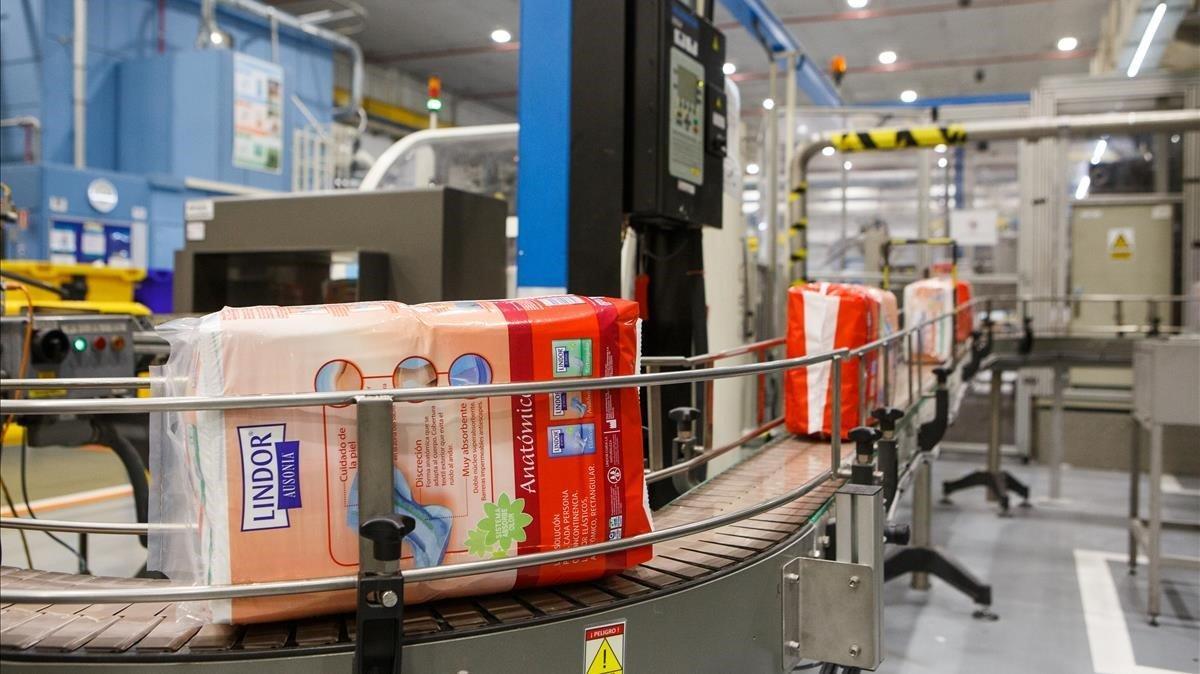
zentauroepp49936435 innovacion191017173326
La planta que elgrup alemany Hartmannté aMontornès del Vallèsha sigut reconeguda pels Enginyers Industrials de Catalunya (EIC) amb el premi a la «millor pràctica empresarial» per implantar lafabricació additiva en 3Da la maquinària, millorant el rendiment i els costos de manteniment. Però si el premi és motiu d’orgull per a l’equip directiu, que ho és, ho és especialment per la història que hi ha al darrere. Perquè lainiciativaguardonada té nom i cognom: Francisco Reyes, eltreballadorque va proposar adoptar aquesta tecnologia.
La fàbrica de Montornès va pertànyer aProcter & Gamblefins al 2017, quan Hartmann va adquirir la marca Lindor, especialitzada en laincontinència adulta, al grup nord-americà. Llavors, l’equip de lideratge de Montornès ja tenia dissenyat unfull de rutaper arribar a lafàbrica del futur, la 4.0, però va aprofitar, fa un any i mig, una aturada de producció per reunir la plantilla, unes 160 persones, i escoltar les sevespropostes de milloraen tots els fronts. Va ser una autèntica pluja d’idees. I va ser en aquest ‘macrobrainstorming’ que Reyes, líder tècnic d’una de les línies d’operacions, va llançar la proposta d’utilitzar la impressió 3Dper fabricar algunsrecanvisde la maquinària.
Dissenyar les peces
Dit i fet. Acceptada la proposta, el mateix Reyes es va encarregar dedissenyar pecesamb el Solidworks, un ‘software’ de disseny assistit per ordinador. «Acumulem ja impreses unes40 peces, i estimem que en un any podrem imprimir-ne un50% més», assegura Xavier López, director d’operacions de la planta.
Ara per ara, la impressió 3D la fa un proveïdor extern, però López no descarta adquirir la impressora quan econòmicament es justifiqui la inversió. I és que l’estalvi, tant en temps com en euros, que s’aconsegueix mitjançant aquesta tecnologia és més que important: un90% en el temps de fabricacióde la peça a substituir i un80% en el cost, destaca el director d’operacions.
També de la pluja d’idees amb els treballadors va sortir la proposta de convertir-se en una planta ‘paperless’,eliminant l’ús del paper i reduint el temps de determinades operacions. I hi estan treballant, no només a Montornès, sinó a tot Paul Hartmann Espanya.
Punts de referència
Aquesta mesura s’emmarca en el programa d’aplicació de lametodologia Lean Manufacturing, en fase molt avançada a Montornès. «Hem sigutpionersa Lean a nivell de grup, i ara estem arrossegant altres plantes a continuar amb aquest model de gestió de la producció», explica Xavier López, que afegeix: «Montornès ha sigut sempre innovació». I tant és així que la fàbrica s’ha convertit en unpunt de referència per a tota la multinacionalalemanya del sector sanitari, coneguda per fabricar lesfamoses tiretes. L’altra fàbrica que Hartmann té a Espanya, concretament aMataró, tampoc es queda enrere en innovació: és uncentre de competència a nivell mundialen el desenvolupament i fabricació de productes sanitaris adhesius, i actualment assumeix laproducció mundial de tiretes.
Notícies relacionadesAmb cinc línies de producció, la planta de Montornès fabrica anualment més de280 milions de bolquersLindor per a incontinència d’adults, una patologia que, sigui dit de passada, afecta el 5% de la població, i un 20% de les persones de més de 40 anys. La producció, ara per ara, es destina al mercat espanyol i portuguès.
La multinacional alemanya té previst invertir 10 milions d’euros entre aquest any i el 2021 en les seves dues plantes catalanes, segons va anunciar recentment el vicepresident d’Europa Occidental i nord de l’Àfrica d’Hartmann, Marc Pérez Pey. La inversió es destinarà principalment a adquirir maquinària per augmentar l’eficiència d’aquestes instal·lacions productives.
- Altes temperatures Dones grans que es confinen per «no morir» de calor: «Em tanco amb un ventilador, tres ampolles d’aigua... i les telenovel·les turques»
- Tips de les residències d’estudiants a Collblanc
- Incendis i tuits frenen Vox
- Els incendis exposen els diferents models de gestió de cada comunitat
- Evacuades més de 100 persones d’un refugi dels Picos de Europa
- Successos Un narco serbi s’amaga set anys a Lloret de Mar i el descobreixen pel passaport fals
- Incendis a Astúries El foc ha arrasat ja 4.000 hectàrees a Astúries: tres nous incendis enfonsen els veïns en l’angoixa
- Les flames avancen i ja calcinen el 7% de tota la província d’Ourense
- Castella i Lleó, Astúries i les Canàries davant el foc
- Sánchez promet ara més mitjans contra el foc i un acord climàtic